AI develops an ultra-light carbon nanomaterial with the strength of steel.
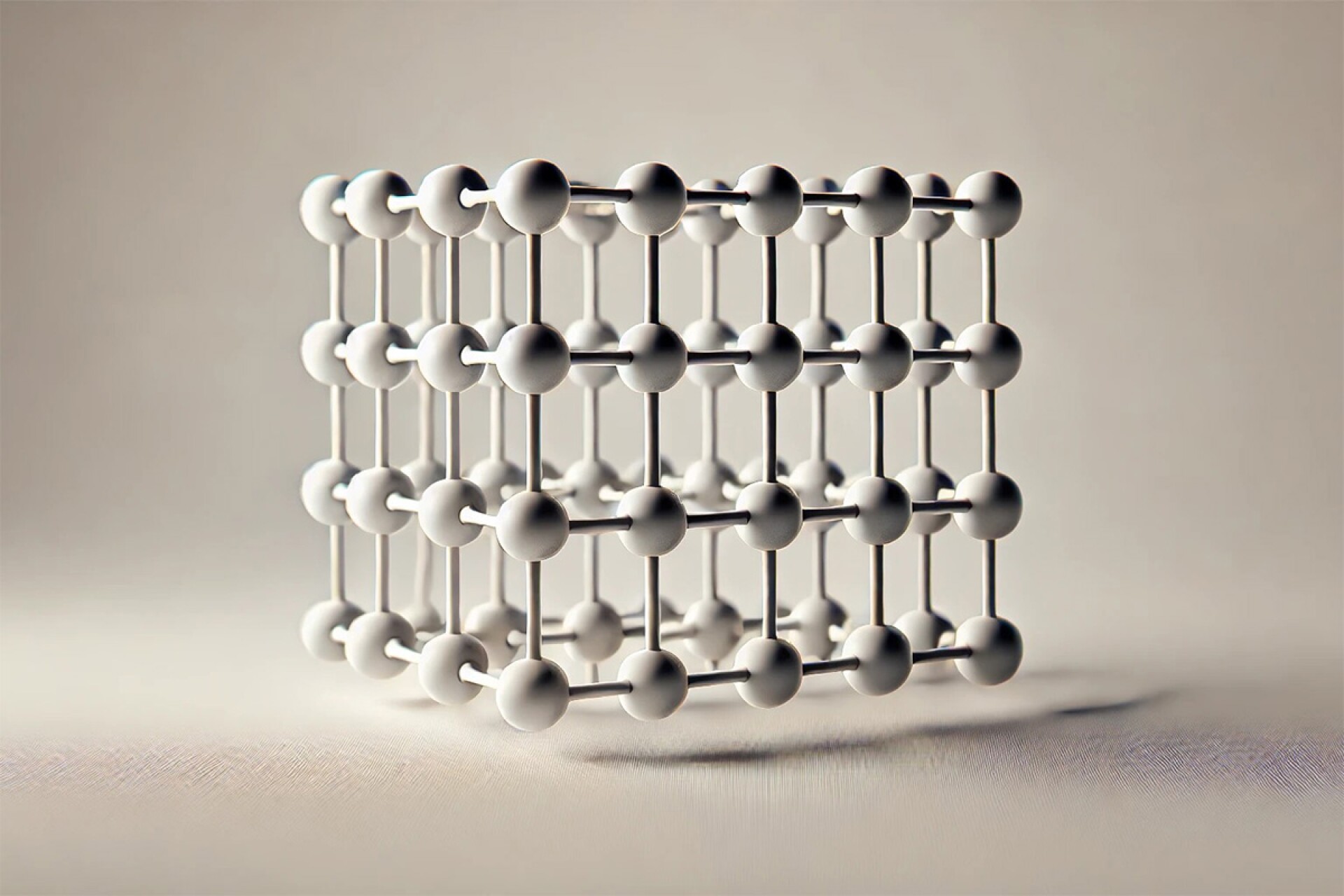
DALL-E
By leveraging machine learning, a Canadian research team has developed ultrahigh-strength carbon nanolattices that rival the strength of carbon steel while remaining as lightweight as Styrofoam.
Last month, the team emphasized that AI had, for the first time, optimized nano-architected materials.Peter Serles from the University of Toronto, a co-author of the study published in Advanced Materials, emphasized the AI’s ability to go beyond replicating existing designs. “It didn’t just mimic successful geometries from the training data,” he explained. “It learned what modifications improved the shapes and what didn’t, allowing it to predict entirely new lattice geometries.”
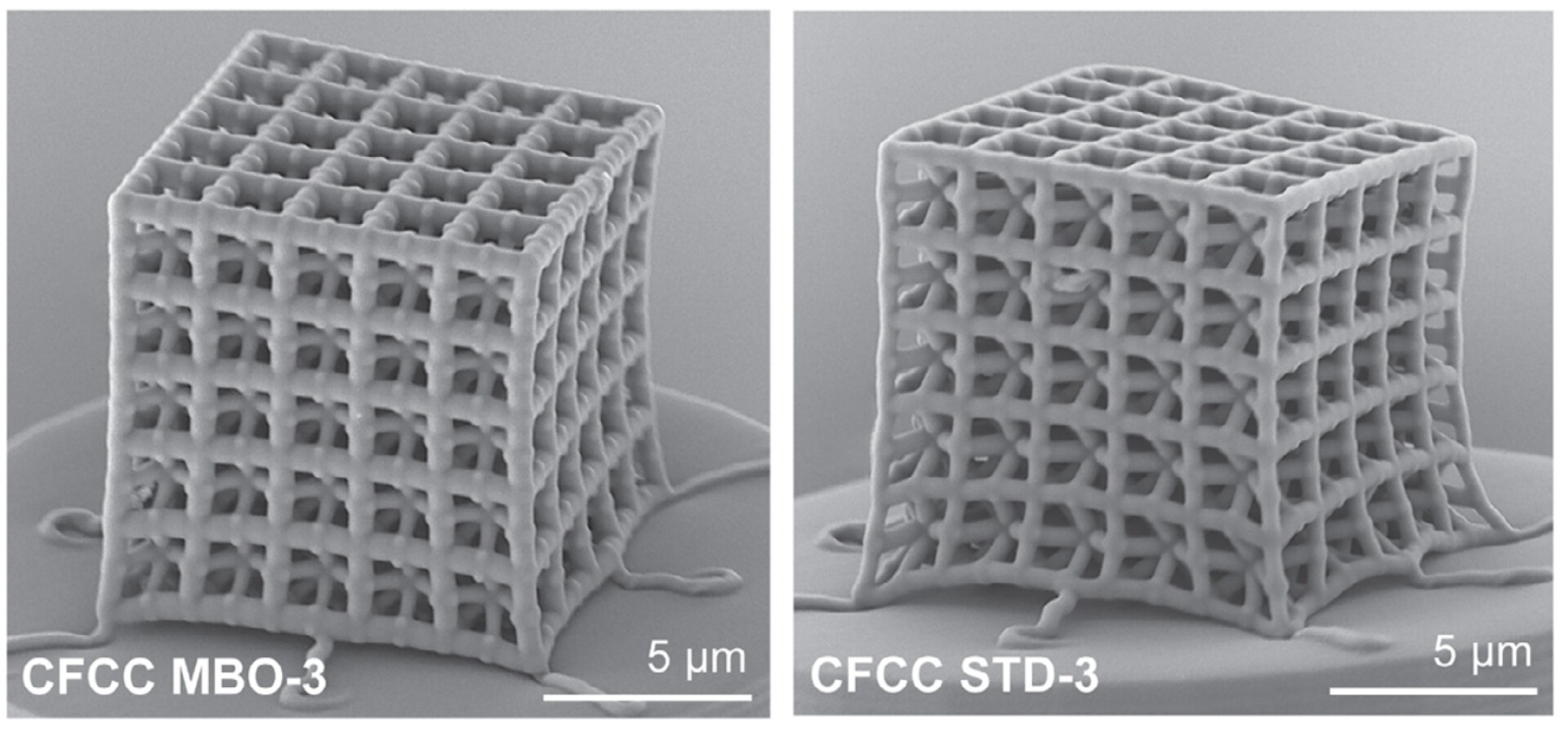
University of Toronto
Nanomaterial design involves precisely arranging atoms or molecules, similar to assembling tiny LEGO structures.Their nanoscale dimensions often give them unique properties. These materials take the form of lattices—ordered, repeating three-dimensional structures that influence their physical, chemical, and electronic characteristics.
AI-Driven Design and Advanced Manufacturing Techniques

Nanoscribe
Working with researchers in South Korea, the team applied a multi-objective Bayesian optimization machine learning algorithm to predict the best lattice geometries. The goal was to enhance stress distribution and improve the material’s strength-to-weight ratio. To bring these designs to life, they used a two-photon polymerization 3D printer, specifically the high-resolution Nanoscribe Photonic Professional GT2—an advanced machine costing hundreds of thousands of dollars.
The resulting nanolattices proved remarkably strong, enduring five times more stress than titanium while remaining lightweight. This breakthrough opens the door for applications in aerospace manufacturing. According to Serles, replacing titanium components in aircraft with this material could save approximately 80 liters of fuel per year for every kilogram swapped out.
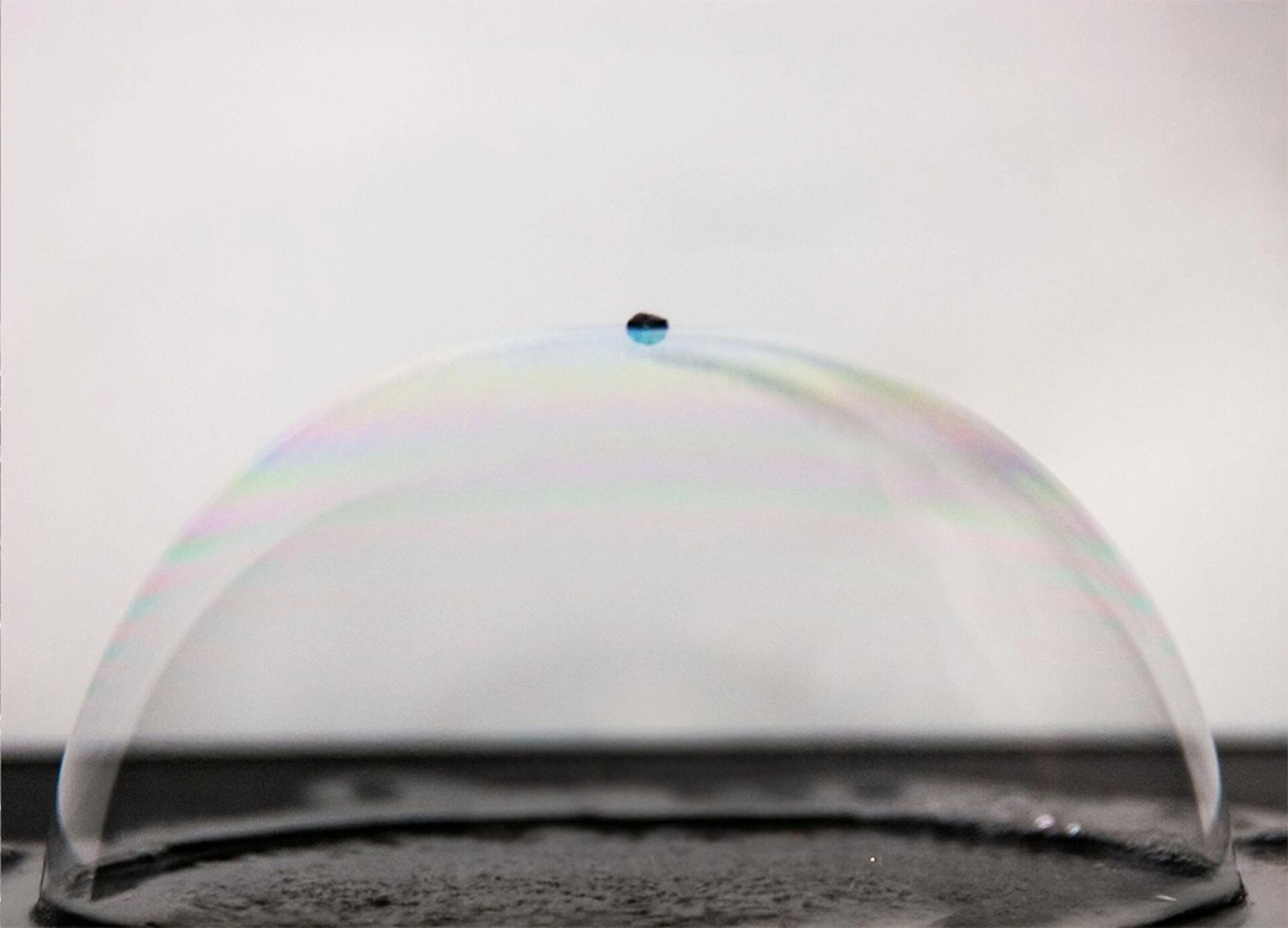
University of Toronto
Looking ahead, the team aims to push the limits even further by creating even stronger, less dense materials. They are also exploring cost-effective manufacturing methods to make large-scale production feasible.
Read Original Article: New Atlas
Read More: Risk of 2032 Asteroid Impact Reduced: Key Details You Should Know