Mobile Factory Makes Lego-Style Bricks from Rubble
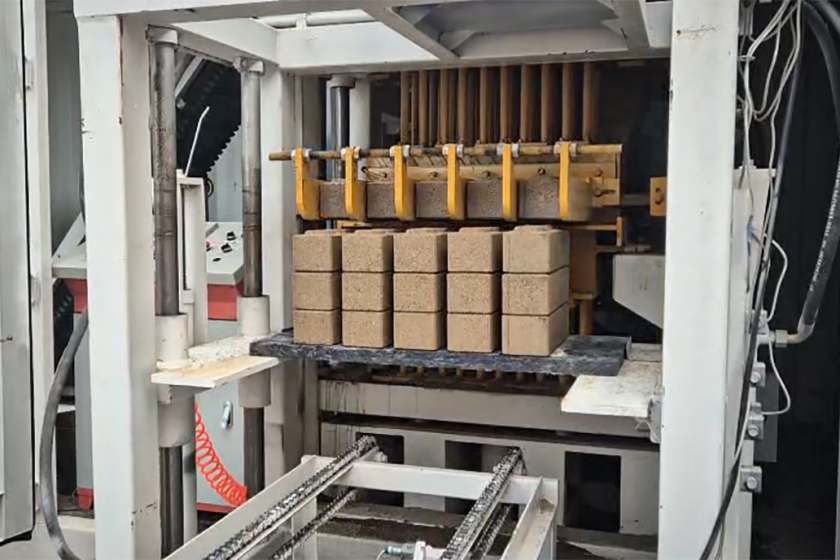
MCC
Wars are adept at turning buildings into rubble, but this mobile manufacturing machine does the opposite: it transforms debris from destroyed buildings into bricks. These bricks can be assembled Lego-style into mortarless structures. After years of development, the first mobile brick factory is heading to Ukraine to assist in rebuilding housing and infrastructure.
Western Australia is becoming known for its advancements in brick-related technology. The world’s fastest brick-laying construction robot, developed by FBR in Perth, recently arrived in the US.
Now, Mobile Crisis Construction (MCC) has also emerged from Perth. Like FBR, MCC has global ambitions. Considering the current state of the world and the rise in natural disasters, MCC’s technology is likely to find widespread applications.
Compact Mobile Factory Converts Rubble into Building Blocks on Site
Housed in a 10-ft (3-m) standard shipping container, MCC’s mobile block factory is compact enough for rapid deployment to disaster areas or war zones, utilizing rubble and waste materials on-site. Although not entirely self-contained, it requires a diesel generator for power and a freestanding hammer mill to crush debris and waste into fine powder.
This powder, combined with a small amount of cement and water, is fed into the machine. Besides rubble, the factory can also use waste materials like plastic bottles, glass, and mine tailings.
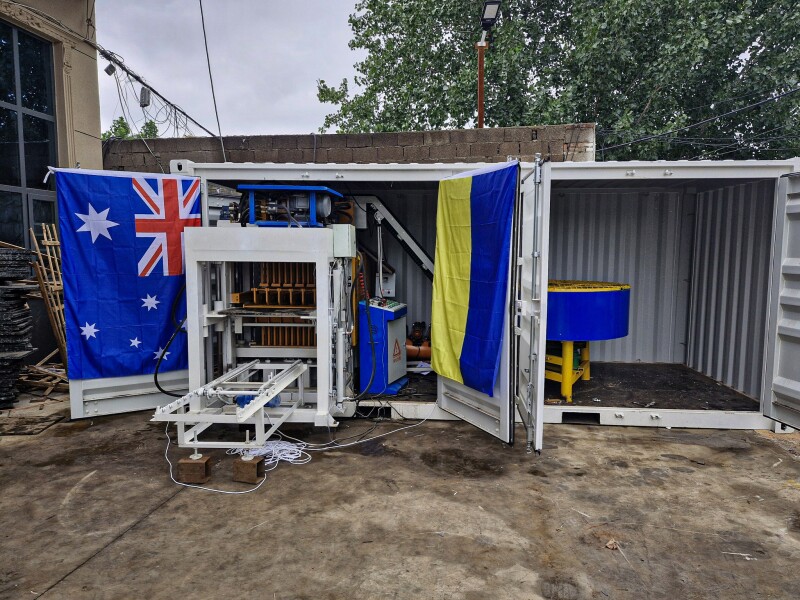
Mobile Crisis Construction
Factory Produces 8,000 Blocks Daily, Enough for Significant Construction Projects
Once operational, the factory can produce 8,000 “Crisis Blocks” or “LayGo Blocks” daily. According to MCC, this output is sufficient to construct one school, three large houses, or ten joined houses per week. Here’s a demonstrator unit rapidly producing blocks:
The clever play on the Lego name is fitting, as these bricks are unique. Similar to their smaller plastic counterparts, they have an interlocking design, enabling them to be laid without mortar—an advantage in areas where mortar may be scarce.
These modular, interlocking bricks come in various sizes, including 100 x 100 mm, 200 x 100 mm, 300 x 100 mm, and 240 x 120 mm. The top mold can be changed to create flat-topped blocks for window sills and wall tops.
If horizontal placement is needed, the factory can also produce pavers of different heights. The bricks require seven days to cure and harden before they are suitable for construction, achieving full strength after 28 days.
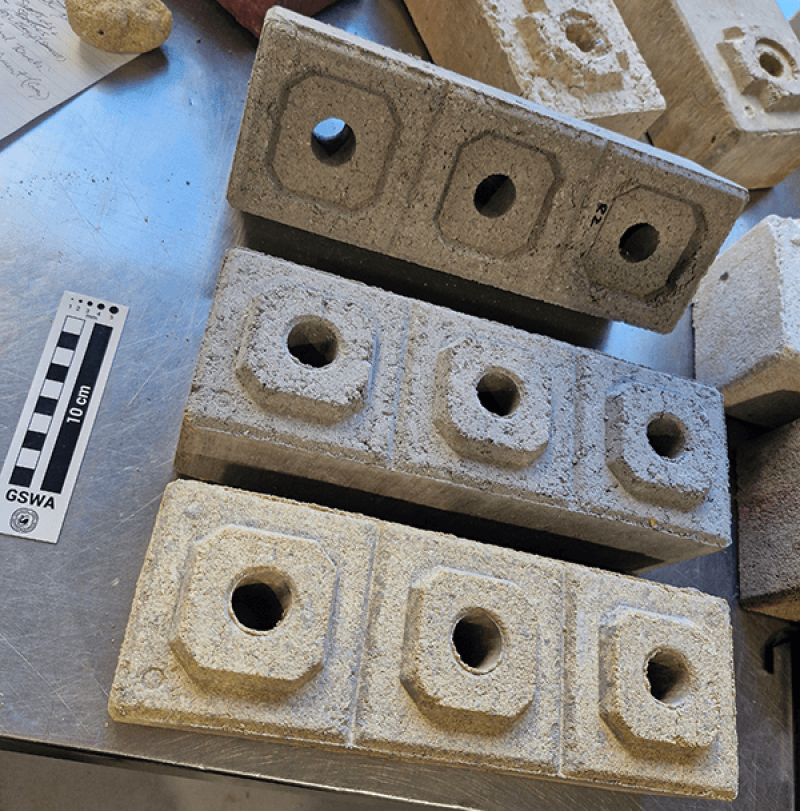
MCC
Mortar-Free Design Simplifies Construction, Enhances Durability
The mortar-free design allows unskilled labor to easily construct walls. The blocks have holes for rebar, which is grouted in place vertically to provide additional strength. The spacing of the rebar depends on the earthquake zone or other structural requirements. MCC claims its blocks, and the walls built with them, are resistant to earthquakes, fire, and cyclones, and even outperform traditional brickwork.
However, constructing a building requires more than just walls. Finishing work, including flooring, roofing, plumbing, fittings, and electrical installations, needs to be completed by local and NGO workers.
It costs AU$120,000 (US$79,000) to send a mobile factory to Ukraine. Thanks to a successful crowdfunding campaign, the first unit is on its way to the war-torn country to help rebuild critical infrastructure and provide emergency shelter.
Initially, it will assist rebuilding efforts in a relatively safe area near Kiev, but MCC aims to expand to other regions. Funding is the main challenge for this expansion, so if you’d like to contribute, you can do so through the company’s website. MCC is an Australian Registered Charity, making donations tax-deductible.
Read the original article on: New Atlas
Read more: Decarbonize 85% of All Industries Using Current Technology