Substitute For Cement Sand Made From Seawater, Electricity, And CO2

Northwestern University
This seemingly simple white paste could be key to addressing the global sand shortage while also transforming the cement production process to capture, rather than emit, carbon dioxide. Researchers at Northwestern University have developed this material using seawater, electricity, and CO2.
Concrete is the most widely used man-made material worldwide, but its production is also one of the most polluting processes. Furthermore, the demand for sand, a crucial ingredient in concrete, is becoming increasingly difficult to meet due to environmental and financial challenges in extracting it from coasts, riverbeds, and seafloors.
A New Material to Address Both Sand Shortage and Carbon Emissions
Northwestern’s innovative material could help tackle both issues. Made of calcium carbonate and magnesium hydroxide in various proportions, this material is relatively easy to create—simply combine seawater, apply electricity, and bubble CO2 through it.
The method mimics how corals and mollusks create their shells, according to the research team.
Here’s how it works: two electrodes in the solution generate a low electrical current that splits water molecules into hydrogen gas and hydroxide ions. When CO2 is introduced, the chemical composition of the water changes, boosting the levels of bicarbonate ions. These ions then react with other natural elements in seawater to form solid minerals that accumulate at the electrodes.
A Versatile Material for Construction and Carbon Storage
The result is a flexible white substance that not only stores carbon but can replace sand or gravel in cement. It can also serve as a base for materials like plaster and paint.
Interestingly, the team found that they could fine-tune the properties of the material by adjusting the flow rate, CO2 and seawater timing, and the voltage and current applied.
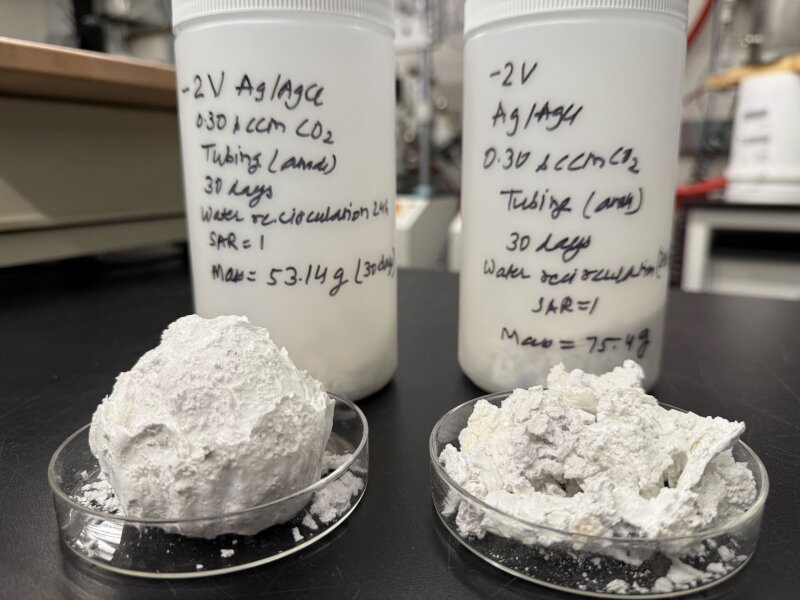
Northwestern University
Alessandro Rotta Loria, the study’s lead author, explained, “We showed that when we generate these materials, we can fully control their properties, such as the chemical composition, size, shape, and porosity. This gives us the flexibility to develop materials suited to different applications.”
This process is far more environmentally friendly than traditional methods. Not only does it reduce the need to mine large amounts of sand, but the only gaseous byproduct is hydrogen, which can be captured and used as a clean fuel. Additionally, the CO2 used could come from cement production emissions, potentially making cement manufacturing greener.
Creating a Circular System for Carbon Capture in Cement Production
Rotta Loria added, We could create a circular system where we capture CO2 right at the source. If concrete and cement plants are located near shorelines, we could use the nearby ocean to feed reactors that transform CO2 into materials using clean electricity. These materials would then become carbon sinks.
Seawater, electricity, and CO2 are abundant and inexpensive resources, and although this process still needs to prove its scalability and commercial viability, it shows promising potential.
If this engineered carbon-capturing sand substitute proves cheaper than transporting natural sand on a large scale, it could significantly contribute to decarbonization. However, it won’t completely solve the problem of green cement by itself. The primary source of carbon emissions occurs during the process of grinding sand with limestone and heating it above 1,400°C (1,670 °K) in a kiln.
Read the original article on: New Atlas
Read more: Mass Production of Floating Nuclear Plants for US Coast