The ISS Successfully Completed the First 3D Metal Printing in Space

ESA/NASA
In an experiment that seems as risky as bobbing for fries, the European Space Agency (ESA) successfully conducted the first 3D metal printing in space aboard the ISS. Developed in collaboration with Airbus, the Metal 3D Printer produced the first of four test shapes.
3D printing on the ISS isn’t a new concept, with the first experiments dating back to 2014. However, those early tests used plastic, which was melted and extruded from a workhead guided by a digital file to form complex shapes. Since the plastic doesn’t reach extreme temperatures, it’s easier to manage, even in the zero-gravity environment of space.
Metal 3D Printing Takes a Giant Leap with Major Safety Modifications
In contrast, the Metal 3D Printer (seriously, they couldn’t think of a more creative name?) operates on an entirely different level. Significant modifications were needed to the standard metal printing process to make it almost safe for use aboard the ISS.
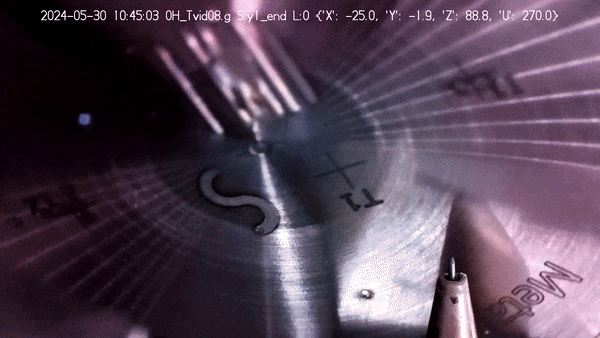
ESA/NASA
Typically, 3D metal printers function by spreading a layer of metal alloy powder, which is then sintered with an electron beam or laser according to a digital pattern. Another layer is added automatically, and the process continues. Once finished, the excess powder is removed, and the product is ready for grinding and polishing.
Innovative Wire-Fed Design Tackles Risks of Metal Printing in Space
Melting metal in zero gravity is already risky, but handling metal powder in space is both hazardous and impractical. To overcome this, the Metal 3D Printer, developed by Airbus and Cranfield University in the UK, uses a process similar to plastic 3D printing. A stainless steel wire is fed into the workhead, where a laser melts it on the spot before it cools and solidifies.
For additional safety, the entire procedure was remotely controlled within a sealed metal box.
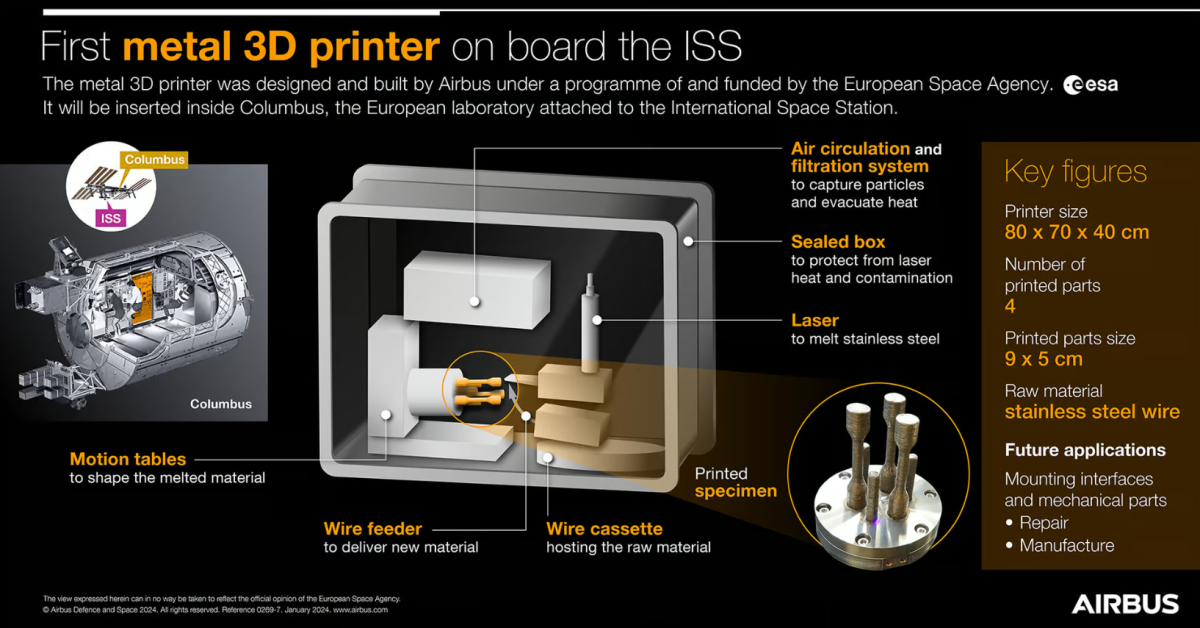
Airbus
First Test Shape Produced by New Printer Marks Key Step Toward Self-Sufficiency in Space
In August, the printer successfully produced the first of four test shapes, though its appearance was far from impressive. It’s rather basic, but the printer is intended as a technology demonstrator, showing how such a device could enable future missions to become less reliant on Earth by allowing crews to manufacture spare parts or equipment themselves.
Once all four test shapes are printed, they will be sent back to Earth for analysis.
“With the successful printing of the first metal 3D shape in space, ESA’s Exploration teams have reached a major milestone in developing in-orbit manufacturing capabilities,” said Daniel Neuenschwander, ESA’s Director of Human and Robotic Exploration. “This achievement, thanks to an international and multidisciplinary team, opens doors for long-distance and long-duration missions where on-demand production of spare parts, tools, and construction components will be crucial.”
Read the original article on: New Atlas
Read more: How to Watch: Launch of the First Private Spacewalk Mission